AMESIM Electromechanical Hydraulic Comprehensive Analysis Software
AMESIM Electromechanical Hydraulic Comprehensive Analysis Software
Amesim can automatically form system equations and perform steady-state, transient or frequency response calculations to analyze system performance.
ABOUT software
Amesim is currently the most widely used one-dimensional multi-domain simulation platform. It establishes mathematical models of physical elements based on dynamic modeling methods and provides professional application libraries for many disciplines, including control, heat, multiphase flow, electrical and electronic systems, Electromagnetic, mechanical and power transmission, dynamics, etc. These professional libraries and library components have undergone extensive engineering inspections. Users only need to connect and assemble the predefined physical component models from various professional libraries according to the system composition to create a complete system model. Amesim can automatically form system equations and perform steady-state, transient or frequency response. Calculate and analyze system performance.

Product Advantage
Amesim is currently the most widely used one-dimensional multi-domain simulation platform. It establishes mathematical models of physical components based on dynamic modeling methods and provides professional application libraries for many disciplines, including control, heat, multiphase flow, electrical and electronic systems, Electromagnetic, mechanical and power transmission, dynamics, etc.
Amesim can automatically form system equations and perform steady-state, transient or frequency response calculations to analyze system performance
Amesim provides powerful secondary development capabilities. Users can develop their own professional libraries or component models, or integrate their existing in-house codes and programs.
Amesim's code generation ability is second to none in similar software. Its excellent code generation and optimization capabilities allow it to easily generate real-time code from the system model, perform hardware-in-the-loop and other hardware-in-the-loop simulations during the design verification stage, and perform control system design plans. Verify and set system parameters.
Application Field
Amesim application of software in engineering
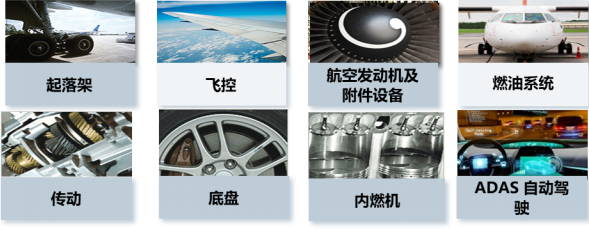
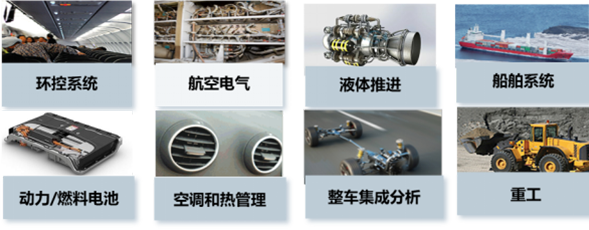
The main function
DesignLife software is composed of at least GlyphWorks basic platform, DesignLife basic platform plus one or more fatigue solvers: The main functional modules are as follows:
Multi-domain modeling, simulation analysis function
- Through the graphical interface, based on the physical characteristics of the analysis object, complex engineering systems such as automobiles composed of multiple disciplines (mechanics, control, multiphase flow, electrical and electronic systems, electromagnetics, power transmission, heat, dynamics, etc.) can be realized , Construction machinery, ships, aircraft modeling and simulation analysis.
Encapsulation function
- Be able to encapsulate the customized component model and encrypt the sensitive parameters of the model.
Secondary development custom function
- It has a dedicated secondary development and customization tool or platform. Based on this tool or platform, a user component model library is created through development. The developed component model can be compatible with the existing models of the software and can be transplanted between different operating systems. This secondary development tool needs to be based on C or Fortran, without the need for users to learn specialized modeling languages.
Time domain analysis tool
- It can realize the time-domain analysis function of the system model, calculate the change curve of model state variables (such as position, speed, etc.) over time, and output it in the form of data file or result curve chart.
Frequency domain analysis tool
- It can realize the frequency domain analysis function of the model, including solving the eigenvalues of the system, drawing the Bode diagram, Nichols diagram, and Nyquist diagram, and performing root locus analysis, modal analysis and order analysis.
Activity index analysis
- The active index analysis can determine the most energy active and the least energy active part of the system model, thereby simplifying the complex system model.
Design exploration tool
- In addition to the interface with third-party optimization software, the software also has a built-in design exploration function, which can directly perform design of experiment (DOE), optimization analysis and Monte Carlo analysis on the system model.
Dashboard function
- The software has a console module with a dashboard. Through this module, you can call pre-defined interactive controls and create pre- and post-processing interfaces. This interface can not only display the calculation results in real time, but also can modify the parameters in real time through this interface to control the simulation operation.
64-bit compilation
- The software must not only be able to run normally on a 64-bit operating system, but also be able to be compiled into 64-bit to improve code calculation efficiency.
Smart solver
- The solver can intelligently and dynamically select the integration algorithm and integration step size according to the characteristics of the system model, and automatically handle the digital stiffness, nonlinearity and discontinuity problems of the system model.
Control system analysis
- Able to build control system models including linear, nonlinear, time continuous, time discrete, conditional operation, composite signal, and hybrid control, and support scalar signals, vector signals, numerical operations and logic operations.
Mechanical system analysis
- It can consider the characteristics of non-linearity and discontinuous points in the mechanical system, such as static/dynamic friction, recoil between mechanical gaps, friction hysteresis, clutch buffering, terminal impact, etc. It has models of mechanical transmission frequently used in hydraulic components, such as lever mechanism, cam mechanism, rack and pinion mechanism, crank connecting rod mechanism, pulley mechanism, worm gear mechanism, ball screw mechanism, thread screw mechanism, etc.
Electromagnetic circuit analysis
- It can analyze the electromagnetic drive circuit composed of armature, energized coil, permeable magnet, air gap and other components, calculate the transient value of physical quantities such as loop magnetic flux, air gap end electromagnetic force, coil current, etc., and simulate the dynamic characteristics of electromagnetic actuators.
Control software interface
- As a complete engineering system simulation platform, Simulink is the de facto standard for control system design. By avoiding the re-establishment of complex multi-domain models and simplifying model exchange on different platforms, users have greatly improved the efficiency of communication between control system design and engineering system design teams.
Thermal analysis
- Heat exchange occurs in most engineering situations, whether it is desired (heater, heat exchanger...) or unavoidable (thermal shock, heat loss, friction...). As long as there is a temperature difference, these heat exchanges may occur through stationary solids or fluids. The heat reservoir handles the heat exchange between solid materials. It is based on transient heat transfer calculation theory for modeling traditional heat transfer modes between solid materials (conduction, free or forced convection, radiation).
Transmission analysis
- The powertrain library contains various modules used to build the powertrain, gearbox and drive train. The library allows designers to consider various physical phenomena involved in powertrain simulation. From engine to tire, the library provides a complete set of modules from the most basic modules to the most detailed advanced modules, providing a complete modeling method for the following applications: design of new automatic transmissions, vibration analysis of drive trains or shafts, change Improvement of gear quality, design of clutch, determination of dual-mass flywheel size, optimization of gearbox efficiency.
Electronics and Power Electronics Analysis
- The library includes two libraries, EB and ESC. The goal of the EB library is to provide engineers in other fields with electrical components covering their needs. Power Electronics Library (ESC) provides all the general functions of power electrical products. Focus on the effective conversion, control and use of static means to regulate electricity, from its effective input form to the ideal electrical output form. The main function provided by the electrical electronics library is that power electronics can easily build converters in the AMESim environment in one click.
Motor and control analysis
- The motor and drive library can be used in most engineering applications where mechanical energy and electrical energy are converted. The motor and drive library is very useful for modern machinery manufacturers and research institutes who need to use electric equipment to replace machinery or drives. This library helps users build a complete electromechanical system simulation model driven by electricity.
Battery and energy storage analysis
- The battery library provides a series of electrochemical batteries and supercapacitor sub-models. The library uses special calibration tools for designing batteries or supercapacitor packages and optimizing their integration in the system, and is widely used for pre-calibration of battery cells (lithium batteries, nickel metal hydride) and general models.